How Should You Choose Copper and Aluminium Lugs?
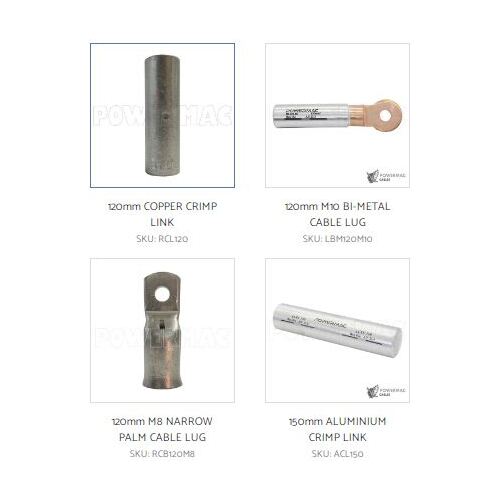

The majority of electrical professionals were still learning about how aluminium has a higher coefficient of thermal expansion than copper. As a result, aluminium-bodied lugs used to terminate aluminium wire were successful while copper-bodied lugs worked as expected. Larger aluminium wires terminated in copper lugs almost always cause problems, whereas using aluminium-bodied lugs reduces those problems, except when moisture enters the lugs.
Corrosion of unprotected aluminium lugs produces aluminium oxide, which causes failure modes in all sizes of aluminium wire. Because of the problems in the past, the electrical industry came to believe that the safest and most dependable way to use wire and lugs was to install an all-copper system. Thus, specifiers required copper conductors, lugs, and bus bars.
Although most electrical equipment manufacturers continue to use copper lugs, a survey revealed that some manufacturers offer equipment with brass lugs, copper-plated steel lugs, tin-plated copper lugs, tin-plated brass lugs, and aluminium-bodied lugs. In fact, some manufacturers produce whatever is specified, whereas others only produce copper, aluminium, brass, or copper-plated steel lugs.
Compression lugs are required in some places, while authorities prohibit the use of mechanical lugs of any metal type. Furthermore, many industrial specifications and even some national standards call for compression lugs that have been fully tinned of copper conductors before being inserted into the lug, and then the lug has been crimped using a full circumference die in a hydraulic crimp tool. This is done in the belief that a compression copper lug is more resistant to corrosion and galvanic action.
A different picture emerges when one looks at the electrical industry in Australia. The majority of the lugs used here have aluminium bodies, but the reliability of modern electrical systems keeps getting better.
What's different now? Is using an all-copper system still the most dependable option? There are still some issues with aluminium-bodied lugs. However, statistically speaking, they fail no more frequently than copper lugs when used in accordance with their design parameters.
In fact, the only aluminium lug failures involved cracking lug sidewalls and threads at the setscrew during initial installation—a problem caused by incorrect torque wrench use.
Because of the thermal expansion properties of copper and aluminium, only aluminium-bodied lugs should be used to terminate aluminium conductors. Similarly, installers can terminate copper conductors with copper- or aluminium-bodied lugs.
Another surprising finding is that manufacturers no longer produce pure aluminium-bodied lugs. Instead, they use a continuous copper or nickel flashing or coating that is covered in tin or silver. Because the tin coating will not adhere to the aluminium, flashing is required. You can see this copper coating on modern lugs by erasing the thin plating with a pencil eraser and revealing the copper underlayer.
When these coatings are not provided by the manufacturer, the formation of a high-resistance aluminium oxide powder occurs shortly after installation, and even sooner in moist conditions. However, the coatings prevent aluminium oxide formation for an extended period of time, even in moist conditions.
When installers use an oxide-inhibiting compound while inserting an aluminium wire (not required for copper wires) into the lug and at the lug area where it connects to the bus bar, galvanic action and oxide formation are almost eliminated, according to the survey. Regardless of whether the wire is made of copper or aluminium, when an aluminium lug surrounds it (as opposed to a copper lug surrounding an aluminium wire), neither the lug nor the wire will deform as a result of temperature changes brought on by current flow.
Manufacturers used to attach rust-prone steel setscrews to aluminium-bodied lugs because aluminium galls or wears away when threaded into aluminium. Applying a polymer wax to the threads prevents the galling of aluminium lugs on aluminium setscrews.
A torque wrench is required because aluminium-bodied lugs crack more easily than copper or steel lugs during installation. Cracking usually manifests itself as thread stripping, which prevents the Allen-head setscrew from securing the lug to the conductor. It could also appear as a crack along the vertical wall of the lug where the setscrew is located.
Another unexpected problem was revealed during conversations with the producers of copper and aluminium lugs: once the bolt with the Belleville washer and the lug setscrew are torqued to specifications, they leave them for life (aside from in the event of a short-circuit event).
This is the opposite of the standard maintenance procedures, which call for lugs to be re-torqued every two to six years. Nowadays, manufacturers advise a thermal scan along with repairs and retorquing only in cases where the thermal scan reveals a heating issue.
The majority of the time, heating is caused by over-torquing the bolt holding the lug to the bus bar, which simply stretches the bolt. The strength required to maintain proper contact between the lug and bus bar to hold the lug in place during a short-circuit event is not present in deformed bolts.
Most installations are still using lugs made of copper, which is still untrustworthy to many. The failure rate of modern aluminium-bodied lugs is not statistically higher than that of copper terminations. This is possible if the aluminium lugs have copper, nickel, tin, or silver coatings; the installers install them with the proper torque wrench values; the aluminium wire is wrapped in an antioxidant compound.
Always contact Powermac Cables for any type of lug you require for your installation anywhere in Australia. With a mission to be the electrical community’s number one choice, they only provide the best quality electrical cables, lights, and accessories across the continent that endure the test of time.